Centralized Distribution
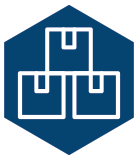
Centralized Distribution
- Storeroom and centralization opportunity
- Source off-site distribution centre for multiple clients
- Preparation of business case for off-site distribution centre
Warehousing and distribution
Logihedron works with multi-site organizations, regional healthcare groups and shared services organizations to develop appropriate and sustainable solutions. These solutions provide environments to ensure optimal patient care focus and efficient operating processes. One of the key services Logihedron offers is the ability to implement, operate and manage a distribution centre for clients (click here for client list). Alternatively, Logihedron can help the client implement a turnkey self-managed solution.
FEATURES
- Feasibility of existing facilities for centralized distribution
- Source and size facility for participating clients
- Assess automation and appropriate storage equipment for facility and client base
- Recommend equipment (storage & machinery)
- Determine costs for a central facility
- KPIs, productivity measures & SOPs established
- Efficient design for facility
- Transition planning services for turnkey projects
BENEFITS
- Space availability for clinical revenue generation
- Efficiency gains to provide additional activity capacity
- Staffing reductions for redeployment or savings
- Distribution of costs among facility users
- Reduction in inventory investment increase in product mix