CASE STUDIES: St. Michaels Hospital | Offsite clinics
St. Michaels Hospital
Offsite Clinics
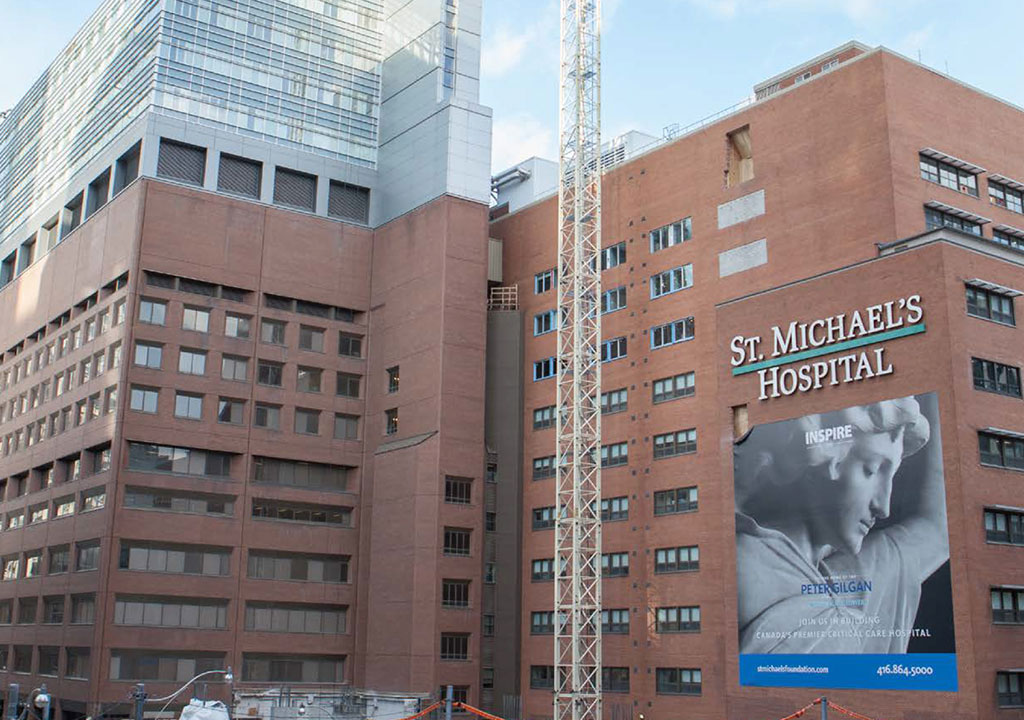
Situation
St. Michaels Hospital operates a number of clinics that are off site from the hospital. These clinics have supply requirements to treat their patients. These supplies were provided by a Supply Store Room at the main hospital site that is operated by the hospital. The store room would order supplies from suppliers, receive, store, pick and deliver to the various clinics. The clinics would place orders to the store-room as supplies would be required, a task usually done by personnel whose primary function was patient care. The ordering from the clinics was a loosely run process with no real responsibilities assigned nor any guidelines to order quantities or frequency of ordering. This led to supply issues at the storeroom as planning for inventory levels was made very difficult due to the ordering practices from the clinics and was a very inefficient and costly process. St. Michael’s hospital also runs a very comprehensive LUM supply program for the main hospital utilizing a central warehouse operated by their SSO (Shared Service Organization).
The SSO has contracted the operation of the warehouse to Logihedron Inc. The hospital has contracted their internal logistics operations to Logihedron Inc. Logihedron supports 140 Clean Supply Areas for the hospital through scheduled replenishment. Logihedron is responsible for the management of the supply areas, product changes and cleaning of the supply carts. Logihedron also reports a number of KPI’s and productivity stats. The hospital was looking at streamlining their inbound supply sources and approached Logihedron to look at adding the off-site clinics to the existing program for the rest of the hospital. This would then eliminate a source of inbound supply and eliminate a parallel process that was providing a similar service. Logihedron agreed to undertake the project and consolidate the off-site clinics into the supply management program at the main hospital.
Analysis and Action Taken
Logihedron firmly believes that in order to have an efficient supply chain, the demand point for products and services needs to be addressed first as this is the initialization of all work required in the balance of the supply chain. With that principle in mind, they embarked on implementing their world class Point of Use Supply Optimization Program. This is an extremely comprehensive ten step program that makes the demand point for supplies highly efficient, user friendly and consistent. The variability is minimized hence allowing the balance of the supply chain to service the demand point much more effectively. As the saying goes “the right product, the right amount of product and the right mix of product at the right time in the right place”
Key steps in the implementation process:
- Ensure items required by clinics exist in the SSO warehouse
- In conjunction with users;
o Review list of products required
o Review quantities recommended for par and minimum
o Agree on space to place supply carts
o Review product grouping on carts
o Agree on service frequency and replenishment day(s)
The clinics were in-serviced by Logihedron, the staff member responsible for the “COUNT” process and “PUT AWAY” process introduced to the clinic staff and communication protocols reviewed with the clinic staff as it relates to supplies. These actions allowed the hospital to gain its objective of reducing the number of inbound supply sources.
Results
The results yielded from this project were both qualitative and quantitative.
Quantitative
- A net reduction in labour from the original situation (difference between what it was costing in the original situation versus the incremental fees from Logihedron)
- Reduction in the number of deliveries to the off-site clinics from the hospital (original situation was 3-5 deliveries per week per clinic, to once a week per clinic)
- Reduction in inventory spend for products, Original situation had items that were non hospital stores items which the hospital had to purchase in the unit of purchase, which usually is a “box” or “case”. When these non-stores items were found to be available in the SSO warehouse, the unit of purchase was usually in low unit of measure or “each”.
- Reduction in storage space. As product is available in low unit of measure, less space is required for storage then the original situation. The additional space can be utilized to add other products the clinic may require.
- Reduction in professional staff hours to manage supplies as a dedicated resource assumes responsibility for supply management and on a scheduled basis. Reallocate hours to patient care.
Qualitative
- Well organized and labelled supply carts reduce care-givers frustration in finding products
- No need to involve professional staff in supply management
- Less congestion of receiving docks during business hours as less vendors delivering at hospital since many items sourced from SSO warehouse instead of vendors.
- Product available in low unit of measure
- Reduced potential for product wastage as a result of obsolescence and expiry due to LUM